Maximizing your foundry’s productivity: installing a runner breaker.
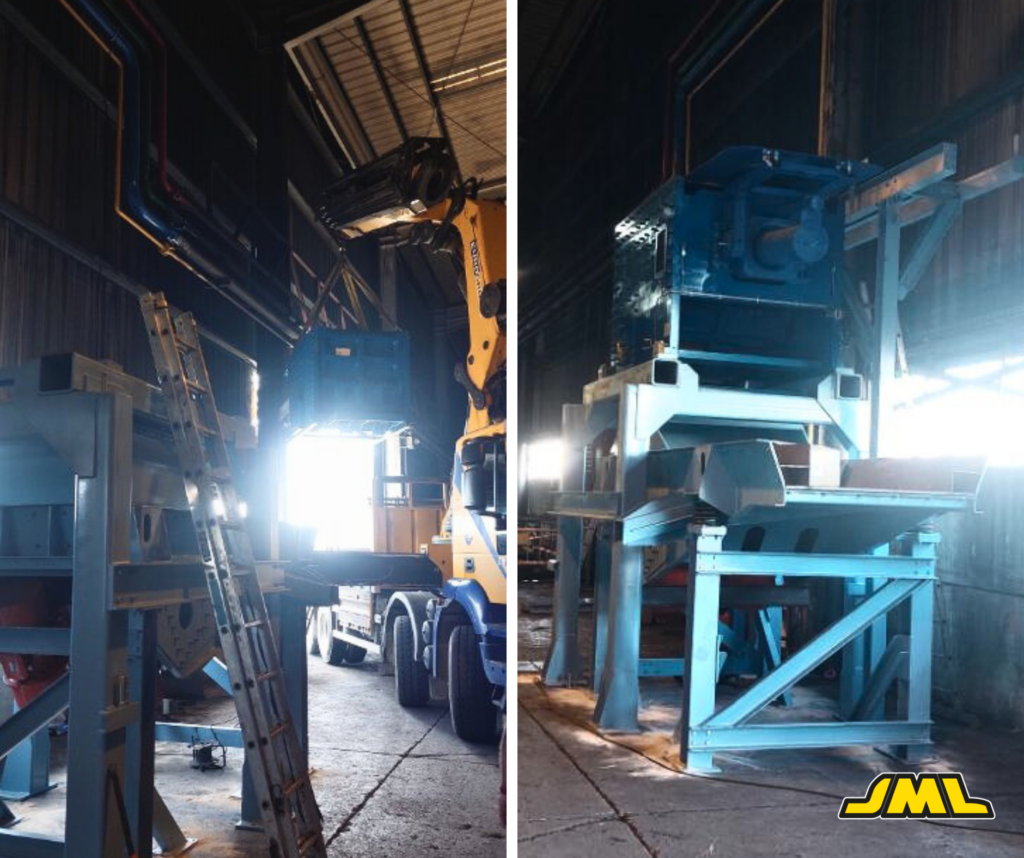
The foundry industry is based on complex processes where every step counts. Our clients, aware of the importance of innovation in improving productivity, quality and profitability, are always on the lookout for innovative solutions. With this in mind, we recently worked with one of our long-standing client to improve its production process with the installation of a high-performance runner breaker. Our solution: a tailor-made runner breaker for optimum results. One of the most common challenges in foundry operations is the management of casting jets, which often require size adjustment. After a careful analysis of our client’s needs and installation, our team of experts designed a custom runner breaker to precisely meet the foundry’s requirements, taking into account the size of the parts to be ground, the required throughput and the quality of the final production. A simple process for impeccable results. The operation of our runner breaker is simple and efficient: castings are transported by a conveyor belt from a vibrating screen to the runner breaker. Inside, the runner breaker performs a precise, controlled size reduction. The advantages of our foundry runner breaker: Benefit#1: Precise, efficient size reduction Our runner breaker offers precise size reduction, a crucial element in ensuring that castings are ready for the next phase of the process, without wasting material. This improvement has a positive impact on the quality of finished products, while generating significant savings in time and costs. Benefit #2: Optimum residue management Below the crusher, a second vibrating screen collects the crushed jets, separating fine sand from other materials thanks to a perforated grid. This function acts like a screen, ensuring that only the necessary elements progress to the skips, reducing waste while optimizing material utilization. Benefit #3: Quick and easy skip changeover Another innovative aspect of our solution is the ease with which the skips can be changed. Mounted on a turntable, skips can be changed quickly and efficiently using a cart, eliminating any loss of time. Benefit #4: Increased profitability At our client’s site, the installation of our foundry runner breaker has led to tangible improvements. Production has become smoother, waste has been reduced and the quality of finished products has risen. These results have had a positive impact on the company’s profitability, strengthening its market position. The installation of a runner breaker at our client’s site is an example of our commitment to working with them to overcome industrial challenges. At JML, we are determined to continue innovating and providing tailor-made solutions to meet the needs of the ever-changing foundry industry. If you would like to find out more about our equipment and services, please do not hesitate to contact us.
Client project : Suction and moisture control of sand
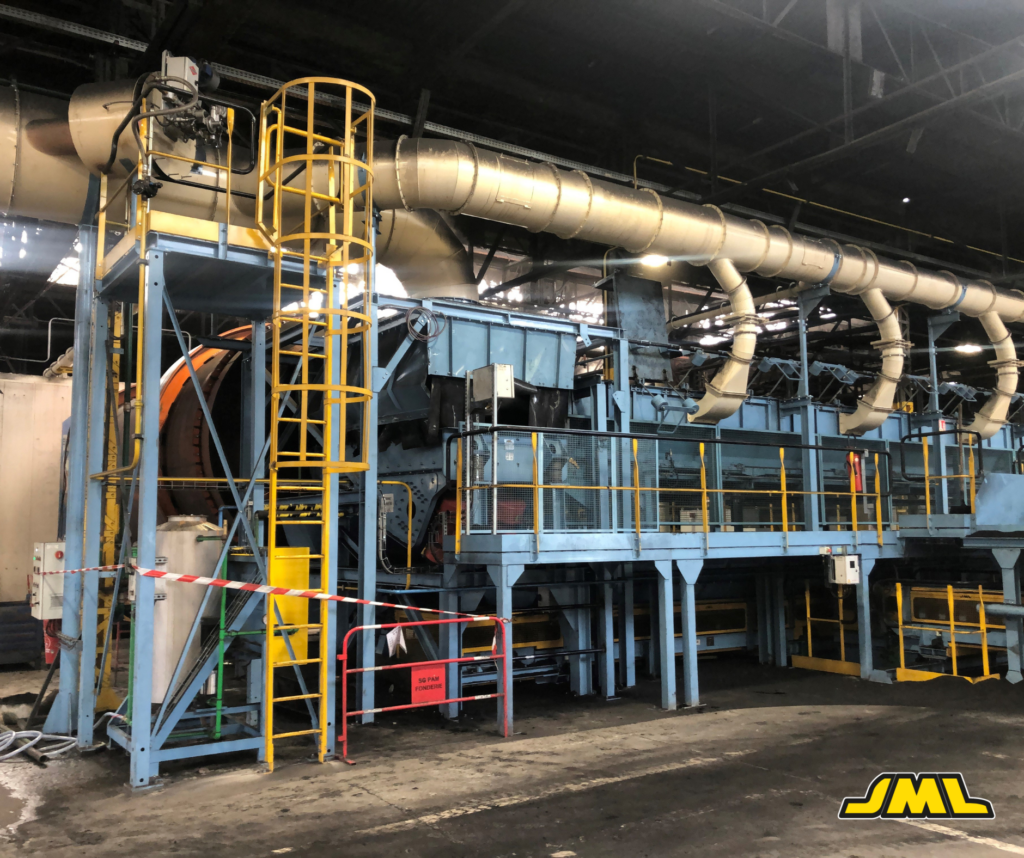
Final phase – Delivery and acceptance of equipment A few months ago, we told you about our latest achievement: the installation of a cooling drum for one of our customers in eastern France. This installation incorporates two specific technology, with the use of a burner within the suction network, the use of a burner within the suction network, aiming to control the suction process and the implementation of our sand moisture management system in the cooling barrel, an essential element of the process molding. Why is sand moisture a major issue in foundry operations? The sand used for molding contain 3% of moisture. When this sand is drawn into the pipes of the suction system, particularly at the level of shake-out, dust loaded with clay associated with humid air can cause blockages and clogging. This reduces suction process efficiency, increases production downtime, and generates unnecessary maintenance costs. Eliminate the moisture with a suction burner To fix this issue, we integrate a burner into the suction network of our client’s sandshop. The main goal is to dry out the air in the suction lines, preventing moisture from disrupting the system’s operations. The burner operates by evaporating excess moisture from the intake air, allowing the dust to circulate more efficiently. Our solution: an automated moisture management system inside the drum We have also set up a device designed by our teams within the cooling drum to manage sand moisture. This system relies on an optimal temperature measurement at the drum inlet, depending on the volume of water initially used. At the outlet of the de-bottlenecking drum, moisture and temperature values are continuously monitored as the sand is transported on the conveyor belt. If necessary, additional water is added in real time to maintain the programmed moisture level. The whole process is fully automated by our teams, which means it requires little maintenance, apart from a periodic check of the moisture sensor to ensure it is properly calibrated. Quality and Economy: Optimize the molding process Implementing a moisture management system as well as the installation of a burner in the dust suctions has many advantages for our client. It optimizes the efficiency of the suction process by reducing obstructions in the pipes, which translates into a significant reduction in production costs. In addition, automatic adjustment of sand moisture ensures consistent molding quality, improving the overall quality of products. If you have any questions or require further information about our moisture management equipment, please do not hesitate to contact us.
In progress Operations
JML is currently manufacturing a cooling drum at his headquater and main production site located in France, Vrigne-au-bois (Grand Est). This equipment is built to shake-out and to cool the sand and will be used by a foundry based in the East of France which produces ductile iron with vertical molding line to optimize their road plate production JML has already installed 6 of them in the last 2 decades Around 6 months are necessary to deliver this equipment as we are now at step 1 (workshop test to ensure all mechanical parts are well assembled). Then step 2 will focus on commissioning on customer site empty test in line with the sand shop test with cold sand during 3 days after 2 weeks of production, optimisation with hot sand We will be proud to share the second step with you next time ! We help your foundry stay ahead by helping you optimise your operations through the right machinery that gives you better results, reduced maintenance and reliable run times.
Dust silos delivered
Environmental requirements require the proper treatment of the dust generated during the foundry manufacturing process. JML offers many technical solutions meeting both the CE and ATEX standards. The images shown below are of a 60m3 stainless steel dust silo to centralize the dust coming from the mechanical regeneration filter and from the mechanical regeneration filter. In this example, the discharge rate is one tanker truck per week. This assembly has eliminated all bigbag handling and protected the operators from diffuse dust during these handlings, in particular thanks to the telescopic sleeve for the transfer of dust from the silo to the tanker trucks.
Three 60m3 silos delivered
We have recently completed a project for a French foundry and have delivered 2 new sand silos and 1 black/bentonite premix silo. Each silo has a capacity of 60m3 and allows the unloading of delivery trucks. The sand and the premix are dosed by a weighing hopper. The entire contents is then sent by pneumatic transport into the sand mixer. We have been working on projects of this type since the decision 4 years ago to further invest in our equipment range. This was a key step and has allowed us to produce silos, chimneys and discharge drums at highly competitive prices without compromising on quality.
PSA Peugeot Citroen optimise the quality of their moulding sand
Et molestie ac feugiat sed lectus vestibulum. Lacus suspendisse faucibus interdum posuere. Ut lectus arcu bibendum at varius vel pharetra.
FBM selects JML
We have completed our FBM’s cooling drum and vibration conveyor device this week. This particular piece of equipment will run at 80 tons per hour. The installation will be completed in September 2018 when the JML team has completed the onsite visit. FBM is a family owned business and is ranked as one of the leading independent foundries in France. With a view of maintaining their position as a highly competitive foundry, they strategically invest in modernizing their production capabilities. FBM commits to injecting 2 million euros annually into production, safety and environment at the group.
Rotating drum delivered to AFC Redon
As part of the modernization of a production line at the foundry of AFC Redon, La Fonte Ardennaise has entrusted its historic partner JML with the replacement of the cooling drum of one of the two molding lines at the Redon site. The technical high level, the flexibility, reactiveness of JML’s technical department are major assets in the choice of this customer. This new equipment will be run September 2017